Build day 3, tail (and maybe a bit more)...
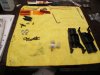
Front gear box parts. Very simple design. No way to set gear mesh, it is what it is. That goes for both the umbrella gear mesh and also the mesh with the slave of the main gear.
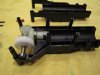
Getting the single umbrella gear into the bearings was pretty easy. Sandwich the bearings in the block halves and press it in. It is fully in when it "snaps" into place. The gears on the shaft, however, were a little trickier.
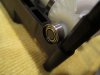
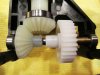
The bearings had to be pressed in so they would pop into the channel. Took a bit of effort and almost missed it, instead letting the bearings ride in top of the raised channel guide on either end. When I went to press the two block halves together it would have been obvious something was off.
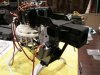
This was a bit of a pain. There are two notches that the block fits into on either side of the frame. It wouldn't line up with the notch holes for quite a while. Took some finessing and swearing to get it lined up. Then the notches wouldn't press into the holes. Ended up having to press pretty hard to get them to go in. Very tight fit, which is good, but unexpected amount of effort needed.
Onto the back block...
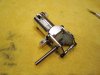
The sub-assembly came very loosely pre-assembled. Nice to have the reference and also makes sure they have all the parts in the baggie.
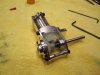
All pulled apart, screws and holes cleaned, and then LT and torqued down.
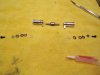
Tail rotor assembly. I find I actually like the rotor head assembly process. Something satisfying about placing all the pieces in the blade grip and torquing it all down. This one was butter smooth, whereas the main rotor grips had that subtle "ripple" to them.
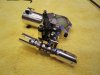
Installed on the tail shaft along with the bellcrank. The small step washers on either side of the bellcrank bearings were a bit of pain. Easy to drop and loose. Got it figured out and assembled though. Very smooth action for rotation and slider movement.
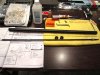
Torque tube time!
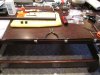
Used some tape on the edge of the table to space out where the bearings would be mounted. Used super glue. Very small bead which I then spread out a bit with the blunt end of a toothpick. Bearings slid on without anything getting in the bearing. After having done it now, I can see how it would be very easy to do so. This is one of those "the less the better" situations.
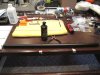
Used a light coating of Break Free CLP (gun lubricant) on the edges of the rubber grommets and slid it in. No problems at all.
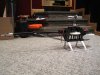
Then it was time to mount it all up. Started by inserting the torque tube into the front block. There is a notch along the left side which is the rough guide for sliding it into place. Tested to make sure the torque tube was engaged with the umbrella gear since it all slid in very easily. Just happened to get lucky that the contact point was aligned perfectly with the gear orientation.

Left the four bolts on the back housing loose for the moment. Then put the tail block on. Once it bottomed out and everything was making tight contact, I backed the rear block off about 1-2mm (the blade 550 build video suggested doing this). Again, I left the two bolts for this assembly loose. Got it up on my steps, balanced it out with some weight on the front, then used a level on the head and on the tail block to make sure they were matched up, which should (hopefully) give a good 90 degree angle between main shaft and tail shaft. I tightened down the front block bolts, checked levels again, then slowly, evenly tightened down the back bolts (after applying some LT). Again, this was a situation where I wasn't sure how much to torque it down. The back block has slots cut into the collar for this connection, allowing the part to compress down on the tube. I didn't go too far with it, afraid I'd crush the tube or damage the tail block. Hopefully it is secure enough. I didn't get any pics of this connection. I'll do that tomorrow to get your guys' feedback. After all this I visually inspected things and leveled them one last time to make sure things were still in line. All good.
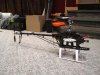
Tail blades mounted (very sturdy plastic). Torqued them down so that there is enough tension to hold them in place in all orientations, but loose enough where at near center there is a +/- 10 degree region where they can move fairly easily. Given the speeds and mass involved, I believe it will be loose enough without being too loose. Mounted tail fin and horizontal fin, torqued down the support rod connection points, hooked up the tail control link to the bellcrank (but guides are still loose until hooked up to the servo).
This looks suspiciously like a helicopter!
Speaking of servos, electronics!
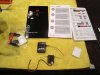
Another manual. Excellent. I eat this stuff for lunch.
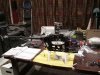
Beginning of some routing planning. Motor wires are very stiff. Nothing taped down or anything yet.
No power for the electronics (no properly sized battery to directly power and no main battery until this coming week. So can't really mount the servo horns or hook up linkages in any way that won't have to be redone later. I can work on routing wires and getting the electronics mounted, but that's about it. Only option I can think of is...
Can I hook a 3S battery to the ESC input and have it power the BEC? the 3S is too much voltage to run directly into the 7200BX, I believe. And I don't have the connectors to make an adapter to the mini-EC connector on the BEC. So I'd have to run it through to the EC5 connector using my "many types" charging cable (put some heat shrink on the bullet connector ends that normally go into the charger). Would this work, or will the ESC only accept 6S?
Will have to check manuals. If it can work then I could potentially get a lot more of this done this weekend.
Otherwise, not much more will be coming until maybe Tuesday or Wednesday when one of the 6S batteries I ordered shows up.
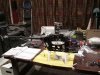