Re: Blade 550 X Pro
Well, hell, now I'm hoping it doesn't suck, too.
So the unboxing and the head assembly...
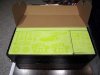
Pleasant green hue. Going from left to right to up...
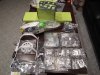
Head, frame, tail boxes and rotor assemblies, along with extraneous stuff (zip ties, blade holders, etc.). Kit includes loctite and a white grease. I had a tube of alternate grease I'm using. Have loctite around here too, but it's out in the other garage so will go with what came with the kit. Well packaged. Each major assembly in its own grouping baggie, containing sub-assemblies within their own baggies. Well marked and matching up with the manual. Manual is very good, with the only exception of not giving much guidance on how much torque to apply on things.
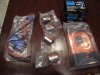
Next sub-box: esc, bec, servos, motor, and receiver/controller.
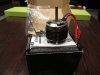
The powerhouse.

Actually was not as large as I was expecting. First time holding and playing with an out-runner motor. The notchiness of the multi-pole magnet setup reminded me of stepper motors.
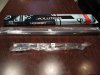
Last sub-box: main rotor blades, torque tube, support rods.
And so it begins... assembly:
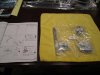
Start with the rotor head assembly.
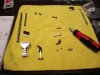
Pull apart the swash driver arms, clean the bolts, apply some loctite and reassemble. I believe one of the bolt holes where the plastic arm connects came cross threaded. Went in difficult. Also possible there was some loctite on there from the factory or maybe a shaving from the thread cutting process. Couldn't get it to go in smooth so just rolled with it. It tightened down fine.
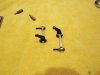
Arms reassembled and ready to go onto the head.
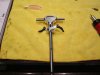
Quickly realized I needed to mount the head on the main shaft since the driver arms, when tightened down, help clamp the head to the shaft to prevent "jittering", of course the main load bearing connection is with the so called "Jesus" bolt. Going to have to find out why it is called that. Probably because when they come loose the pilot can do nothing but pray.
Getting the dampers in there was a bit of a pain. There is a plastic collar on the feathering shaft between the dampers so you can't just press the dampers into the head and then slide the shaft through. At least one of the dampers has to be pressed into the head after it is on the shaft. (This is just full of innuendo.) I now realize I should have used the blade grip to help push the damper into place. As it was I used the blunt side of a set of needle nose pliers to finesse them into place.
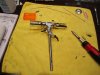
Forgot to take a pic of the bearing and washer layout. Nothing special anyway. Greased up the bearing cage, open end toward the spindle to help prevent the stuff from just running out on spin up. I didn't have a second 3mm hex head key available so I'll probably have to break the loctite and resecure the assembly tomorrow. I did manage to get it torqued down alright, to the point both the blade grips were a bit "notchy" when rotating them. But with the way the dampers are just press fit into the hub, I'm pretty sure there is some more play to tighten out of it. I suspect sitting overnight they will settle in a bit too, allowing for a bit more tightening to occur.
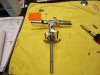
Left the cap off the top for the time being since I'd need to remove it anyway later on for blade pitch measurements. Popped the swash onto the driver arms. I'll be unpopping tomorrow and backing all the ball ends off the swash and reapplying loctite to make sure they are secured. Actually I'll go do that now before crashing for the night.
Got a couple of batteries ordered up and on the way (one EPBuddy 35C and the other a Turnigy 30C, non-nano-tech). Along with some EC5 connectors and an EC5 paraboard. They had 4mm bullets in stock too, so ordered up some of them to keep around.
Need to go get some wet sanding paper tomorrow so I can start in on the frame!
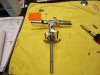