Heliman450
Well-Known Member
Hi all, latest photos to update you all............
All the Supra X connections ready to prepare for the great soldering event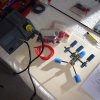
Positioning of batteries to measure up for changeover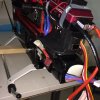
Option #1
Option #2 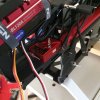
Option #3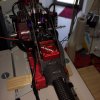
Options 1&2 are the standard Align proposals for positioning the gyro. Option #3 seems to fit the Axon instructions of fitting it close to the main rotor and away from the buzzing stuff. It also has the advantage of not needing to extend servo wires but does need the ESC supplies extending.
All feedback appreciated.
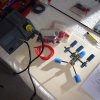
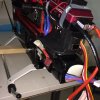
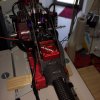
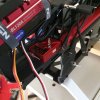
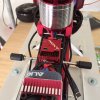
All the Supra X connections ready to prepare for the great soldering event
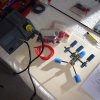
Positioning of batteries to measure up for changeover
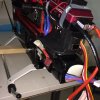
Option #1
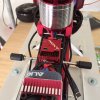
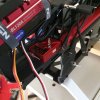
Option #3
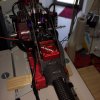
Options 1&2 are the standard Align proposals for positioning the gyro. Option #3 seems to fit the Axon instructions of fitting it close to the main rotor and away from the buzzing stuff. It also has the advantage of not needing to extend servo wires but does need the ESC supplies extending.
All feedback appreciated.
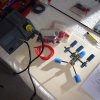
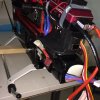
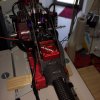
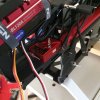
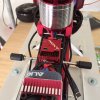
Last edited: