coolgabsi
Super Mod & DEAL KING!
So , as you guys have seen in my signiature, one of the three helis I have is a VIBE 50. IT is a heli made by JR. JR made some bad birds (esp in the 600 nitro class) but then they copied ther JR VIBE 90 design to make a 50 and it was extremely sucessful. And then they copied Vibe 50 deisng to deisng Vibe 90 SG .. haha.. When it came out , it was one of the best nitro 600 helis in the market. The heli inherently is reviewed to fly on rails, and rightly so, man it tracks .. I can let push my sticks one way and draw a straight line.. it WILL FOLLOW! its a freaking train.. Its a bit heavier than its counterparts like Aling TREX 600 and Miniature Furion 50, Velocity 50 (outrage) etc, but it is quality bird. It was all the hoot when it came out , and Curtis youngblood then was a JR team pilot and he flew and tested all its prototypes.
Thats the history..
So, people who have Vibes love them to death. and ofcourse, who doesnt want more POWER!! HAHA.. so I researched and found someone had tried to stuff a YS91 in the Vibe before sucessfully. and they loved the power.. Now obviously the 90 engine drinks fuel, but heck if I cna get 6 moinuites of pure power.. HEY !! Thats good. The mod they had done was keeping the same gear ratio of 8.7 on the drive train.. which I will address later.
So the modding is simple.. I should say Simpler (or tony will kill me
) .. So The equipment needed:
1) OS 91 HZ engine (DUH lol .. or any 90 size engine.. they make them pretty standard in dimensions.. )
2) Vibe 90 (NOT VIBE Scott Gray or SG .. ) engine mount .. as I explained above, there are tow Vibe 90 variants.. The engine mount you need comes from the Vibe 90 (V9) not Vibe 90SG (VSG)..
http://www.horizonhobby.com/products/engine-mount-v9-JRP996075
3) A Vibe 50 fan hub, and collets. (you can use the one that you already have.. or get another one.. )
4) 11T pinion from Vibe 90.
THATS IT!!!!!!!!!!
So mod:
The engine crankshaft is longer than a 50 size engine .. so it needs to be shortened by approximately 3mm.
The fan hub : the inner diameter of the hub is meant for a 50 size engine. The Fan hub hole needs to be drilled bigger.. This needs to be done VERY carefully as this hub is rotating 16000RPM.. and if the hole is not straight, the heli will eventually shake it self apart.
Different configs call for different washer config.. For example, an OS engine needs only one Prop washer, while Vibe manual calls for two in YS. Play with that, to see what fits best for your engine. I have a prop washer in my mine, and that makes the prop nut screw on the hub just enough so it had a good loctite hold on it. (LOCTITE is what holds your hub to the puller, the screw and threads by themselves arent enough.. )
After that is all done, mount the engine on the new 90 engine mount, install the clutch on it, and stick it in the clutch bell. Line it up and mark holes so the engine mount can be mounted square on the body. .The engine mount will need to marked with the mounting points, and that can be a bit tricky.. as you might have to play with that to get the right hole config.. Mine had to be done in a way that the holes were oval as they didnt quite coincide with the stock holes but were half way there..
Once the holes are marked , the mount will need to be centerpunched. through and through .. so the screws can go through and hold the mount..
OK so the gear ratio.. the Vibe 50 comes with a 10T pinion and a 87T main gear making it a gear ratio of 8.7. GREAT TORQUE for a 50 engine, but a bit too much for a 90.. It wont have the rpm I desire, and will probably end up stripping my main gear as the OS 91 engine makes about double the amount of torque a 50 would. The first mod that was done ran with the stock drive train and they had the engine basically screaming at 17000++ rpm .. the practical rpm of the engine is 16000 for OS and 17000 for YS. They never reported a faliure, but I wasnt confortable enough to run the engine that high rpm or 1700-1800 headspeed on the head ..
OS 91 HZ is rated at maximum power at 15000 RPM and maximum practical rpm 16000 RPM
15000/8.7 = 1724 power band
16000/8.7 = 1839 MAX
So now we install the 11T pinion.. That will make the gear ratio 87(main gear) / 11t pinion = 7.909
15000/7.9 = 1898~~~ 1900rpm power band
16000/7.9 = 2025 ~~~ max
BIG difference.
So I can essentially run the engine at 1900-2000-2100 rpm on Normal - ID1 -- ID2 . Why higher.. cause the head rpm drops when load is applied, so we try to run higher than powerband so when rpm drops it falls into power band and makes continous sweet sweet power..
so that said.. we need the 11t pinion installed.. The pinion installation ::::::::::::::::::::::::::::::::::::::::::::::::::::: (TONY ADDS THIS )
Once pinion is installed on the clutch bell, mount the engine, and you will notice that the backplate of the 90 sticks lower than the bottom plate. So, what you would do, is just carve out the bottom plate shape from the bottom plate, and mount on the bottom plate.
Hook it all up, get the governor set, make sure the new gear ratio is in there and throttle linkage is set right.. and thats it
So did I do all this myself.. (LOL) NO!! I am not a good machinist and not to mention dont have a shop as I live in apartments. So TONY came to my rescue.. All the work done above was dont by Tony.. He machined it all, did all the painstaking installation and modifications and MAN he has done a GREAT JOB! I coudnt have done it without his help. All the KUDOS go to him for making this possible. I just paid for the parts, boxed it up and shipped it to him
and told him basically what needed to happen. and magic happened there in the middle HAHAHAH..and couple weeks later I had my bird back
SO here it is all installed. I will ask if tont has some more pics of him doing any of this work. I can post the final product ..
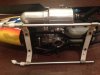
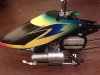
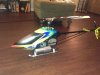
Tell you what.. the MUFFLER LOOKS HUGE on this heli !! and man ! the heli looks sweet!
cant wait to maiden it!
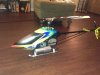
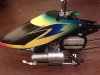
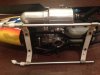
Thats the history..
So, people who have Vibes love them to death. and ofcourse, who doesnt want more POWER!! HAHA.. so I researched and found someone had tried to stuff a YS91 in the Vibe before sucessfully. and they loved the power.. Now obviously the 90 engine drinks fuel, but heck if I cna get 6 moinuites of pure power.. HEY !! Thats good. The mod they had done was keeping the same gear ratio of 8.7 on the drive train.. which I will address later.
So the modding is simple.. I should say Simpler (or tony will kill me
1) OS 91 HZ engine (DUH lol .. or any 90 size engine.. they make them pretty standard in dimensions.. )
2) Vibe 90 (NOT VIBE Scott Gray or SG .. ) engine mount .. as I explained above, there are tow Vibe 90 variants.. The engine mount you need comes from the Vibe 90 (V9) not Vibe 90SG (VSG)..
http://www.horizonhobby.com/products/engine-mount-v9-JRP996075
3) A Vibe 50 fan hub, and collets. (you can use the one that you already have.. or get another one.. )
4) 11T pinion from Vibe 90.
THATS IT!!!!!!!!!!
So mod:
The engine crankshaft is longer than a 50 size engine .. so it needs to be shortened by approximately 3mm.
The fan hub : the inner diameter of the hub is meant for a 50 size engine. The Fan hub hole needs to be drilled bigger.. This needs to be done VERY carefully as this hub is rotating 16000RPM.. and if the hole is not straight, the heli will eventually shake it self apart.
Different configs call for different washer config.. For example, an OS engine needs only one Prop washer, while Vibe manual calls for two in YS. Play with that, to see what fits best for your engine. I have a prop washer in my mine, and that makes the prop nut screw on the hub just enough so it had a good loctite hold on it. (LOCTITE is what holds your hub to the puller, the screw and threads by themselves arent enough.. )
After that is all done, mount the engine on the new 90 engine mount, install the clutch on it, and stick it in the clutch bell. Line it up and mark holes so the engine mount can be mounted square on the body. .The engine mount will need to marked with the mounting points, and that can be a bit tricky.. as you might have to play with that to get the right hole config.. Mine had to be done in a way that the holes were oval as they didnt quite coincide with the stock holes but were half way there..
Once the holes are marked , the mount will need to be centerpunched. through and through .. so the screws can go through and hold the mount..
OK so the gear ratio.. the Vibe 50 comes with a 10T pinion and a 87T main gear making it a gear ratio of 8.7. GREAT TORQUE for a 50 engine, but a bit too much for a 90.. It wont have the rpm I desire, and will probably end up stripping my main gear as the OS 91 engine makes about double the amount of torque a 50 would. The first mod that was done ran with the stock drive train and they had the engine basically screaming at 17000++ rpm .. the practical rpm of the engine is 16000 for OS and 17000 for YS. They never reported a faliure, but I wasnt confortable enough to run the engine that high rpm or 1700-1800 headspeed on the head ..
OS 91 HZ is rated at maximum power at 15000 RPM and maximum practical rpm 16000 RPM
15000/8.7 = 1724 power band
16000/8.7 = 1839 MAX
So now we install the 11T pinion.. That will make the gear ratio 87(main gear) / 11t pinion = 7.909
15000/7.9 = 1898~~~ 1900rpm power band
16000/7.9 = 2025 ~~~ max
BIG difference.
So I can essentially run the engine at 1900-2000-2100 rpm on Normal - ID1 -- ID2 . Why higher.. cause the head rpm drops when load is applied, so we try to run higher than powerband so when rpm drops it falls into power band and makes continous sweet sweet power..
so that said.. we need the 11t pinion installed.. The pinion installation ::::::::::::::::::::::::::::::::::::::::::::::::::::: (TONY ADDS THIS )
Once pinion is installed on the clutch bell, mount the engine, and you will notice that the backplate of the 90 sticks lower than the bottom plate. So, what you would do, is just carve out the bottom plate shape from the bottom plate, and mount on the bottom plate.
Hook it all up, get the governor set, make sure the new gear ratio is in there and throttle linkage is set right.. and thats it
So did I do all this myself.. (LOL) NO!! I am not a good machinist and not to mention dont have a shop as I live in apartments. So TONY came to my rescue.. All the work done above was dont by Tony.. He machined it all, did all the painstaking installation and modifications and MAN he has done a GREAT JOB! I coudnt have done it without his help. All the KUDOS go to him for making this possible. I just paid for the parts, boxed it up and shipped it to him
SO here it is all installed. I will ask if tont has some more pics of him doing any of this work. I can post the final product ..
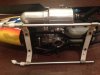
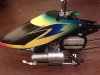
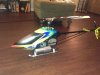
Tell you what.. the MUFFLER LOOKS HUGE on this heli !! and man ! the heli looks sweet!
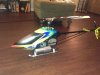
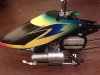
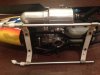