As you will have noticed my previous post is missing many of the pictures so I am posting from the point the pictures are missing again, hopefully everything will be ok this time
The next job was fitting main landing gear onto the wings, the holes for the leg brace and the main leg fixing point are hidden under the wing covering as shown in the instruction, the small holes for the wire supports are easily found by feeling with your finger, I found that it was necessary to adjust the wire at the bends to allow the ends to fit into the holes easily, this wire is high tensile and I had to use a vice to hold it close to the bend that needed tweaking and use a hammer to make small adjustments, once the wire ends are correctly adjusted and fitted there is a plastic strap that is screwed down to hold the wire leg support in place. Fig 6
Fig 6
When I test fitted the suspension leg and plastic strap in place I found that the plastic strap was too wide and pushed the leg back against the wire which prevented the leg from raking forward and connecting with the 2 bracing straps, I solved this problem by making a smaller strap from some metal I had although smaller using metal has made it stronger, Fig 7
I also found that the 2 angled plates that hold the suspension leg to the wing were wider than the recess in the wing, I managed to slide one side between the wing surface and the ply fixing surface the other side I had to cut a recess in the wing surface to accommodate the extra length of the side angle plate. Fig 8
Fig 7
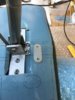
Fig 8
I next test fitted the wheel into the to the landing gear leg, again I needed to adjust things, firstly the 2 pieces of flat bent metal that form the brace between the wire and the leg were badly out of shape and needed twisting and the bends adjusting so that they met the U sides of the leg evenly, luckily the metal is mild steel so bending was quite easy. Fig 9
Fig 9
The wheel is held in place by a length if rod that is threaded at each end this is passed through the suspension frame and wheel there is a collar either side of the wheel which holds the wheel central these are held in place by grub screws, the rod is held in place by a nut at each end, when I test fitted this together I found that in order for the sprung leg to operate correctly the U section of the leg and the flat support pieces need to be able to move easily, I found for this to work correctly it required the nuts to be loosely tightened and they were only on the bolt by a couple of threads , obviously this is not acceptable the nuts would fall off during the first flight, the answer would be to use nilock nuts unfortunately the rod is not long enough to accommodate nilock nuts Fig 10
To get over this problem I used a bolt of the same thickness and ground the head of the bolt to reduce its size and cut it to the right length to use a nilock nut, to prevent the thread from wearing wheel centre I used an epoxy filler to fill the threads Fig 11
This worked quite well, the nilock nut should be shake free and the sprung leg moves freely Fig 12
Fig 10
Fig 11
Fig 12
I have now started fitting the wheel and suspension covers, I noticed that the wheel boot was quite flimsy around the edge so I reinforced around the edge about 2 inches wide with fibre glass matting, it is now really strong and should withstand any landings that may end up in long grass etc Fig 13
Fig 13
The main wheel boot is a bit fiddle to get over the metal work but once over there is quite a bit of movement room, a bit of rubbing down of the edge of the wing fairing was needed to get it to fit to the wing shape as much as possible, once the wheel boot is slipped into the fairing there is plenty of adjustment to get the wheel central in the boot before gluing, one quite important part of finishing the suspension is final fitting of the wheel, the instruction manual shows the bolt being pushed into place over the edge of the boot Fig 14, I tried every way I could but was unable to manage to get the bolt in place like this, I eventually had to drill a hole in the boot to get the bolt in place, I’ll sort the hole later, the wheel is a snug fit in the boot but the suspension moves perfectly without snagging Fig15
Fig 14
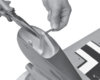
Fig 15
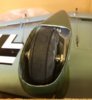